The Essential Guide to Precision Molding in Metal Fabrication
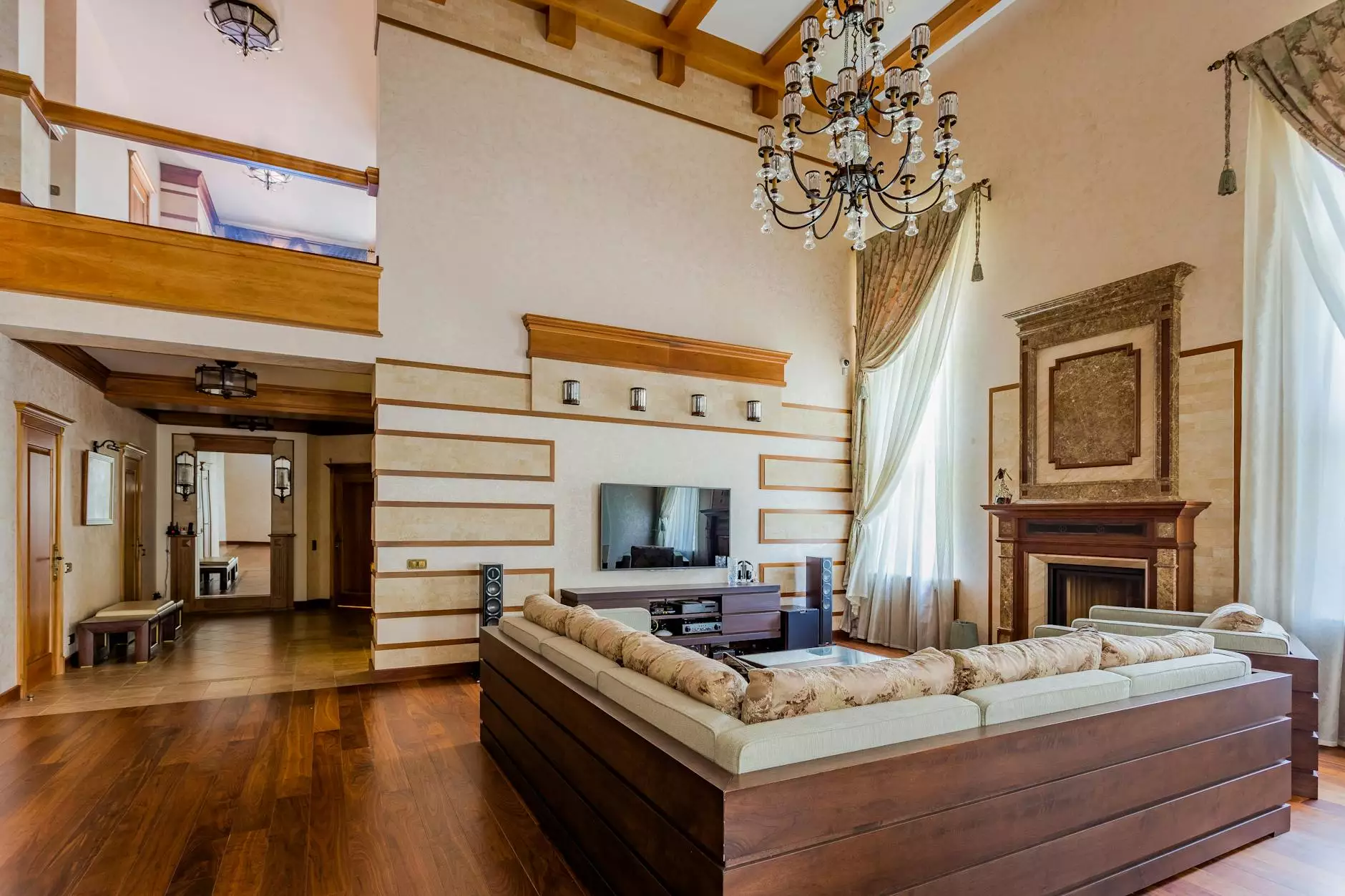
In the dynamic world of manufacturing, precision molding stands out as a key innovation that has transformed how products are developed and produced. This detailed exploration delves into the fascinating domain of precision molding, its applications, and its indispensable role in the metal fabrication industry.
Understanding Precision Molding
Precision molding is a highly sophisticated process that allows for the creation of metal components with extreme accuracy and consistency. This method involves the shaping of materials—typically plastics or metals—using a mold, which defines the final product's shape and features. The precision attained through this process is unmatched, making it invaluable in sectors such as automotive, aerospace, medical equipment, and consumer electronics.
Key Characteristics of Precision Molding
- High Tolerances: Precision molding can produce parts with tolerances as tight as ± 0.01 mm, ensuring that each component fits perfectly in its intended application.
- Complex Geometries: Molding techniques allow for intricate designs that would be impossible to achieve through traditional manufacturing methods.
- Material Versatility: A wide variety of materials can be molded, from lightweight plastics to durable metals, making it suitable for various industries.
- Consistency: Each part produced is consistent in quality and specification, minimizing waste and maximizing efficiency.
- Cost-Effectiveness: While initial set-up costs can be higher, precision molding can lead to reduced production costs in the long run due to less material waste and labor.
Applications of Precision Molding in Metal Fabrication
The applications of precision molding in metal fabrication are vast and varied. Here are some crucial areas where this method is particularly beneficial:
1. Automotive Industry
In the automotive sector, precision molding is essential for producing components that require a high degree of precision, such as engine parts, gears, and housing units. Metal fabricators utilize this technique to create lightweight yet durable components that contribute to overall vehicle efficiency.
2. Aerospace Engineering
Aerospace applications demand the utmost precision and reliability. Here, precision molding is employed to manufacture critical components like brackets and housings for electronics. The lightweight nature of molded parts helps improve fuel efficiency without compromising safety.
3. Medical Devices
The medical industry relies heavily on precision molding for creating devices that are not only accurate but also biocompatible. Surgical instruments and implantable devices must meet stringent regulations, making this method a perfect fit for production.
4. Electronics
In the tech domain, precision molding is used to create housings for gadgets and components that require exact dimensions for proper functionality. As electronics continue to shrink in size, the role of precision molding becomes even more critical.
Benefits of Precision Molding for Businesses
For businesses involved in metal fabrication, adopting precision molding techniques leads to numerous advantages. Here are some of the most significant benefits:
Increased Efficiency
The molding process allows for rapid production cycles with minimal lead times. This efficiency contributes to a quicker time-to-market for products, giving businesses a competitive edge.
Reduction of Material Waste
Unlike traditional machining methods, which often result in significant material waste, precision molding utilizes materials more effectively, leading to cost savings and a reduced environmental footprint.
Enhanced Quality Control
Precision molding ensures that each part produced meets strict quality standards, reducing the likelihood of defects and the associated costs of rework or scrap.
Customization and Flexibility
Modern molding techniques are highly adaptable, allowing for rapid changes in design and production runs without extensive downtime. This flexibility is crucial in a fast-paced market where customer preferences can shift quickly.
Choosing the Right Precision Molding Partner
Choosing the right partner for precision molding can make a significant difference in the outcome of your projects. Here are key factors to consider:
Experience and Expertise
Look for partners with a proven track record in metal fabrication and precision molding. Their experience can provide valuable insights and enhance the quality of the final product.
Advanced Technology
Ensure that your partner utilizes the latest technologies and machinery for molding. State-of-the-art equipment can significantly impact the quality and efficiency of production.
Quality Assurance Processes
Confirm that the partner has stringent quality control processes in place. This guarantees that every piece of equipment produced meets the necessary safety and performance standards.
Customization Capabilities
Your partner should be able to accommodate custom designs and specifications. This flexibility is crucial, especially if your needs evolve over time.
The Future of Precision Molding
The future of precision molding looks bright, with ongoing advancements in technology and materials. These developments are likely to drive innovation in the following areas:
1. Sustainability
With growing environmental concerns, the precision molding industry is focusing on sustainable practices. This includes the use of eco-friendly materials and processes that minimize waste.
2. Industry 4.0
The integration of smart technology, including IoT and artificial intelligence, into the molding process is set to enhance automation and efficiency, paving the way for more agile manufacturing systems.
3. Continued Customization
As consumer preferences become increasingly specialized, the ability to customize components through precision molding will be paramount. This trend will drive innovation as manufacturers seek to meet unique customer needs.
Conclusion
Precision molding is not merely a manufacturing technique; it embodies the future of metal fabrication, offering unparalleled accuracy, flexibility, and efficiency. As industries continue to evolve, embracing precision molding can position businesses at the forefront of innovation, enabling them to respond to market demands swiftly while maintaining the highest quality standards. By choosing the right partners and adapting to the latest technologies, businesses can harness the full potential of precision molding to enhance their product offerings and drive success in an increasingly competitive landscape.
Visit deepmould.net for more information on how precision molding can elevate your manufacturing processes and transform your business.